激光打孔技术对氧化铝陶瓷微观结构的影响
激光打孔技术,作为现代制造领域的关键技术之一,以其精度高、通用性强、效率高、成本低等综合优势,在众多材料加工中发挥着重要作用。氧化铝陶瓷,以其高硬度、优异的抗磨损性和耐高温性能,成为众多高科技领域的核心材料。本文将深入探讨激光打孔技术对氧化铝陶瓷微观结构的影响。
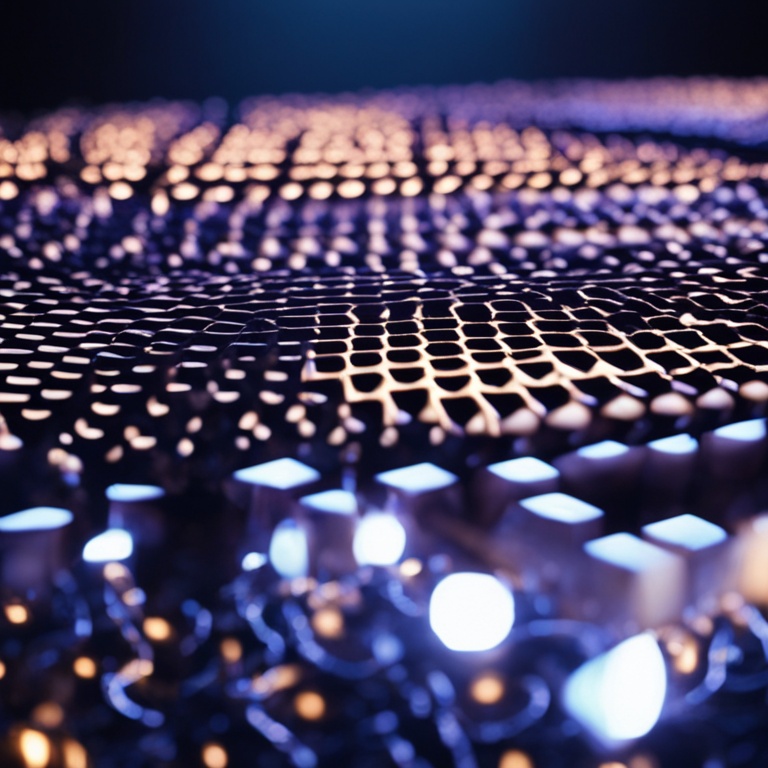
激光打孔技术基于激光束的高度集中性和高能量密度,通过聚焦后的激光作为高强度热源对材料进行加热,使激光作用区内材料融化或气化继而蒸发,从而形成孔洞。这一过程在氧化铝陶瓷上同样适用,但由于其硬脆特性,传统加工方法往往难以达到理想的加工效果。激光打孔技术则能够克服这一难题,实现高精度、高质量的孔洞加工。
在激光打孔过程中,激光参数如平均功率、扫描速度、扫描次数等,对氧化铝陶瓷孔洞的微观结构有着显著影响。以紫外纳秒激光为例,研究表明,随着激光平均功率的增加,孔入口直径随之增大,这主要是由于激光能量增大使得氧化铝陶瓷加工区域吸收的热量增多,烧蚀区域体积扩大。然而,孔出口直径的增幅相对较小,这可能与已成型的孔通道和通道内的等离子体反射部分激光能量有关。此外,扫描速度和扫描次数也会影响孔洞的形貌和尺寸。
激光打孔对氧化铝陶瓷微观结构的影响不仅体现在孔洞尺寸上,更在于孔壁形貌、重铸层及裂纹等方面。孔壁形貌是评价激光打孔质量的重要指标之一。在激光打孔过程中,由于激光束的高能量密度和快速加热作用,孔壁往往呈现出熔融、再凝固的形貌特征。这种形貌特征对于氧化铝陶瓷的导电性、热传导性等性能可能产生影响。
重铸层是激光打孔过程中形成的另一种微观结构特征。它是指在激光作用下,熔融的材料在孔壁周围重新凝固形成的一层材料。重铸层的厚度和性质对氧化铝陶瓷的性能有着重要影响。较厚的重铸层可能导致材料性能下降,如硬度降低、抗磨损性减弱等。因此,在激光打孔过程中,需要控制合适的激光参数,以减少重铸层的形成。
裂纹是激光打孔过程中需要特别关注的问题。由于氧化铝陶瓷的硬脆特性,激光打孔过程中容易产生热应力和机械应力,从而导致裂纹的产生。裂纹不仅影响材料的力学性能,还可能成为材料失效的源头。因此,在激光打孔过程中,需要采取一系列措施来减少裂纹的产生,如优化激光参数、选择合适的加工路径等。
近年来,复合激光打孔技术为氧化铝陶瓷的激光加工提供了新的思路。通过结合纳秒激光和毫秒激光的优势,复合激光打孔技术能够在无激光吸收剂、高压气体辅助下实现高速、高质量的打孔。这一技术不仅提高了打孔效率,还优化了孔洞的微观结构,减少了重铸层和裂纹的形成。
综上所述,激光打孔技术对氧化铝陶瓷微观结构的影响是多方面的。通过优化激光参数、选择合适的加工路径以及采用复合激光打孔技术等手段,可以实现对氧化铝陶瓷高精度、高质量的激光打孔加工,为高科技领域的发展提供有力支持。