氧化铝陶瓷激光打孔工艺中的质量监控技术
氧化铝陶瓷,以其高硬度(莫氏硬度8-9级)和低导热性,在电子封装基板、传感器元件及精密结构件等高精度需求场景中广泛应用。然而,这些特性也为激光打孔工艺带来了诸多挑战。为确保加工质量和效率,质量监控技术在氧化铝陶瓷激光打孔工艺中显得尤为重要。
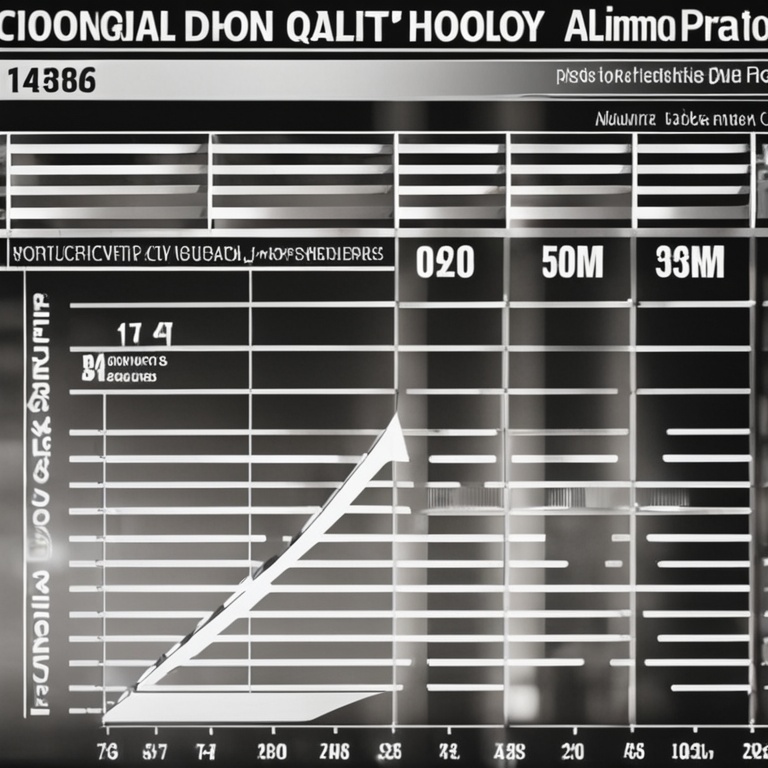
一、激光打孔工艺概述
激光打孔是利用高能量密度的激光束,瞬间将氧化铝陶瓷材料熔化和汽化,从而形成孔洞。这一过程具有加工速度快、精度高、非接触式加工等优点,能有效避免陶瓷材料因受力而产生的裂纹问题。然而,激光打孔设备价格昂贵,运行成本较高,且对操作人员的技术要求也非常高。
二、质量监控技术要点
1.工艺参数优化
激光打孔的工艺参数,包括激光功率、切割速度、脉冲频率、脉宽及辅助气体等,对加工质量有着直接影响。
- 激光功率:功率不足会导致切割不透或打孔粗糙;功率过高则可能引起边缘崩裂、基体熔融飞溅。因此,需根据材料厚度和孔径需求精确调整激光功率。
- 切割速度:速度过快易导致熔渣残留;速度过慢则会造成热累积,增加裂纹风险。合理的切割速度应确保材料均匀受热和有效去除。
- 脉冲频率与脉宽:高频脉冲能分散能量,减少热损伤;而超快激光的短脉宽可忽略热影响,适用于精密加工。辅助气体的使用,如压缩空气或氮气,有助于吹除熔融物,减少氧化和裂纹产生。
2.缺陷预防与应对
氧化铝陶瓷激光打孔过程中常见的缺陷包括边缘崩裂、孔壁粗糙、切割不完全和基板裂纹等。这些缺陷的成因复杂,需采取综合措施进行预防。
- 边缘崩裂:主要由热应力集中和功率过高引起。可通过降低功率、提高切割速度和使用超快激光等方法进行预防。
- 孔壁粗糙:脉冲频率低和辅助气体不足是导致孔壁粗糙的主要原因。提高脉冲频率至80kHz以上,并增大气体压力,可有效改善孔壁质量。
- 切割不完全:焦点偏移和功率不足是导致切割不完全的常见原因。需定期校准焦点,并根据材料特性调整激光功率。
- 基板裂纹:冷却不足和切割路径突变是基板裂纹的主要成因。增加水冷装置和优化切割路径,避免直角转折,可降低裂纹风险。
3.高精度加工策略
为实现氧化铝陶瓷的高精度加工,需采用先进的加工策略和设备。
- 自动对焦系统:确保不同厚度基片的焦点精度,提高加工稳定性。
- 高精度运动平台:满足微米级孔位精度需求,确保加工精度和一致性。
- 分阶段切割:对于复杂图形,采用分阶段切割策略,先切割内部小孔,再加工外轮廓,减少材料释放应力,降低裂纹风险。
三、结论
氧化铝陶瓷激光打孔工艺中的质量监控技术涉及多个方面,包括工艺参数优化、缺陷预防与应对以及高精度加工策略。通过精确控制激光功率、切割速度、脉冲频率等关键参数,采用先进的加工设备和策略,可确保氧化铝陶瓷激光打孔的高质量和高效率。随着技术的不断进步和应用领域的拓展,氧化铝陶瓷激光打孔工艺将在更多领域发挥重要作用。
本文版权归网站所有,转载请联系并注明出处:
http://www.yiylaser.com/article-detail/NMw9Kjdb